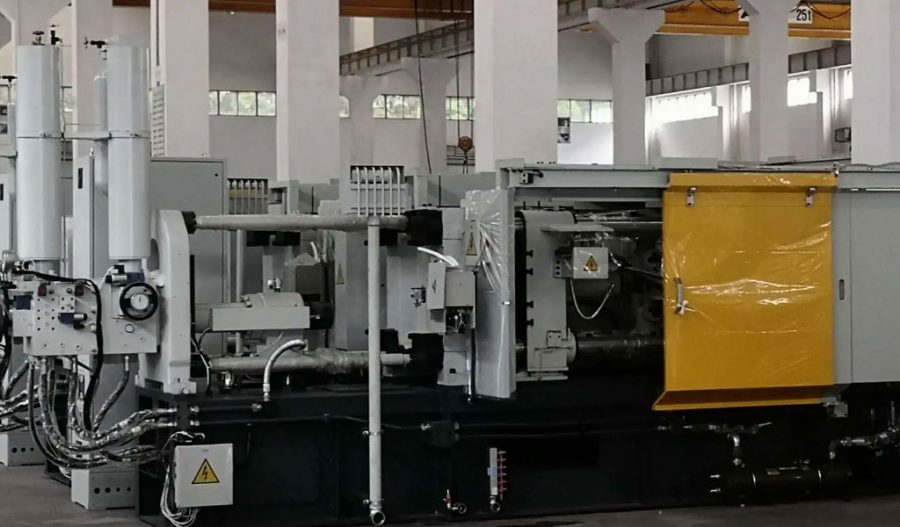
Getting your product from the drawing to a tangible version is a crucial aspect of design. Without it, you have no way to test and validate your design before it’s finalized for mass production. Die casting is one of the ways you can bring your designs to life. It involves die casting – molds manufacturing – CNC machining, which delivers high precision, fast, and durable prototypes of parts from a billet or block of your chosen material that is cut with a series of drill bits and tools.
Are you considering die casting for your project? Be sure to consider these Key Elements to Consider Before Proceeding before you proceed:
Die Casting Materials
Die casting allows you to volume make your model with almost all kinds of materials that can withstand heat and stress. Some of the most popular materials used are aluminum, zinc, and special alloy like magneium and copper.
Die Casting Machining methods
Die casting uses the cavity of the mold to apply high pressure to the molten metal. Molds are usually machined from stronger alloys, a process somewhat similar to injection molding.
Your Die Casting project
Die casting is used typically for volume building high-quality prototypes for functional testing. However, it’s also practical for crafting custom casts or molds to build prototypes for other production processes, such as injection molding. In this case, the CNC machining prototyping process also qualifies as rapid tooling.
Die Casting Tolerances
CNC machines can be very accurate, but running the mill on the highest accuracy can be time-intensive and costly. That’s why tolerances are used, and these are measurements indicating the level of precision required for the prototype you’re making. In short, they represent the degree of variation permitted in the measured value or final dimensions of the part. Reputable providers of CNC prototyping and edm wire cutting services control their tolerances to DIN-2678-1 Medium for Fine for metals.